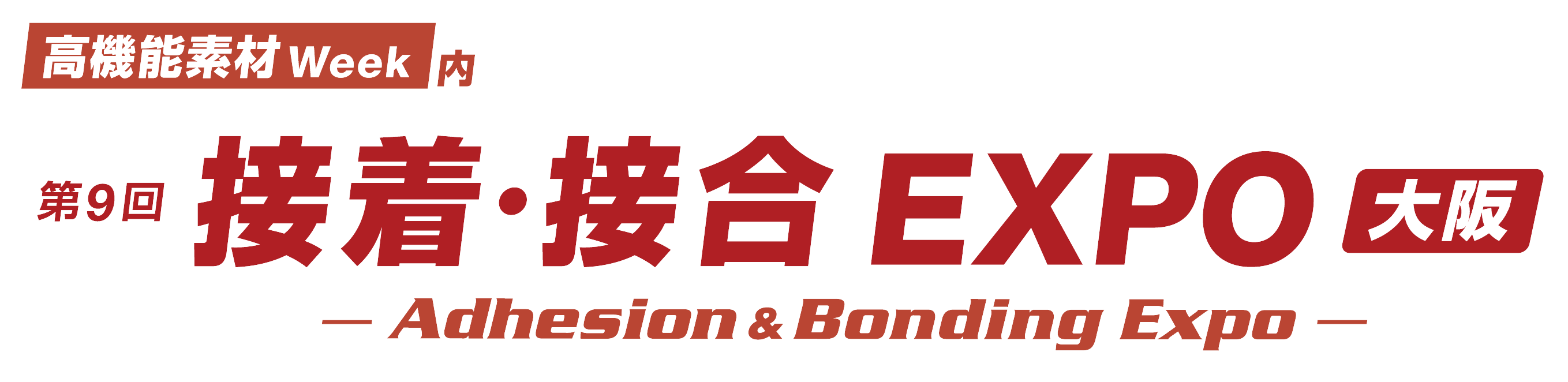
ヒートシンク形成、パワーモジュール接合、DMB接合、フレキシブル基板接合、超音波カットサンプルを展示
来る2025年5月14日(水)よりインテックス大阪で開催される【大阪展】高機能素材Week内 第9回接着・接合EXPOに出展いたします。(4号館、ブースNo.18-78)
展示会では超音波応用技術として、ヒートシンク形成、パワーモジュール接合、DMB接合、フレキシブル基板接合、超音波カットの紹介を行います。
また、弊社装置で加工した様々な分野のサンプルを多数展示いたしますので、新しいアイデアの実現や課題解決のお役に立てるものと思います。
ご来場の際はぜひ弊社ブースへお越しください。 事前来場登録制となりますので、こちらよりご登録をお願いいたします。
【展示サンプル紹介】
<ヒートシンク形成技術>

1.ピン接合(写真左、中央左)
●DBC基板にピンを半田やTIMを介さずに形成できるため、熱伝導率が高くなり放熱性能が向上します
●一度に最大4ピンまでの同時接合ができ、プログラマブルにピンを配列できるため、
引抜き材と比べてヒートシンク形成の自由度が向上します
●ピン形状は丸ピンだけでなく、水の流れを考慮したひし形ピンの接合も可能です
2.リボンボンディング(写真右)
●プログラマブルにリボンを配列できるため、引抜き材と比べてヒートシンク形成の自由度が向上します
●DBC基板にリボンを半田やTIMを介さず形成できるため、熱伝導率が高くなり放熱性能が向上します
●装置はマルチフィーダーを搭載されており、リボンの材質や幅、厚みなどを自動切換えすることが可能で
量産対応を実現します
3.ブロックフィン接合(写真中央左)
● 引抜き材のヒートシンクフィンを、半田やTIMを介さず形成できるため、熱伝導率が高くなり放熱性能が向上します
● DMBシートを接合材料の間に挟むことで、引き抜き材のようなサイズの大きな材料も接合が可能となります
【関連装置】
・ピン接合 :超音波ピン接合装置PB2000MS
・リボンボンディング:超音波リボンボンダ RB300SS
・ブロックフィン接合:超音波金属接合装置 UB5000/3000/2000LS
<パワーモジュール接合技術>

1.端子接合(写真左)
●ターミナル端子とDBC基板を半田等の中間材料を介さずダイレクトに接合できるため、
接続抵抗が低くなりエネルギー損失による熱の発生を大幅に減らすことが可能です
●常温で接合が可能で半田のように熱をかける必要がなく、基板上の電子部品にダメージを与えません
●接合時間は1秒程度と短く、タクトアップを実現します
●ローダ・アンローダ付き装置での量産実績が国内外問わず多数ございます
2.パターンなし・極小パターンでの端子接合(写真右、中央右)
●パワーモジュールの端子接合では、接合時に発生するヒゲバリや屑の低減が求められています
●DMBシートを接合材料の間に挟むことで、パターンのないフラットなホーンで接合できるため、
接合界面からのヒゲバリの抑制にも効果が期待できます
3.基板間接合(写真中央左)
●ワイヤーに比べて1本あたりの電流をより多く流せるリボンでの基板間接続を実現します
●装置はマルチフィーダーを搭載されており、リボンの材質や幅、厚みなどを自動切換えすることが可能で
量産対応を実現します
【関連装置】
・端子接合 :量産用超音波金属接合装置TB1000MS
・基板間接合 :超音波金属接合装置 UB5000/3000/2000LS
<DMB(Dot Matrix Bonding)接合技術>

DMB工法とは、材料表面に微細な突起を形成したDMBシートを接合材料の間に挟み接合する工法です。
シートに形成された突起が接合起点となり、通常よりも接合時の面圧を向上させることができるため、材料同士が接合されやすくなります(写真左)
1.有機基板上へのハーネス接合(写真中央左)
●通常の超音波接合では、接合時の熱でデラミネーションが発生、基板にダメージを与えてしまいます
●DMB接合であれば接合条件の緩和により熱の発生が抑制できるため、基板にダメージを与えず
太電線の接合が可能となります
2.ディスクリートデバイス(写真中央右)
●ディスクリートデバイスへ放熱板を超音波接合すると、振動によりデバイスの破壊が懸念されます
●DMB接合であれば接合条件の緩和により超音波振動を抑制、デバイスの破壊を防ぎます
●放熱板の厚みは、最大5mm程度まで接合が可能となります
3.大面積接合(写真右)
●通常の超音波接合ではサイズ□20mm程度の接合が限界でしたが、DMBシートを接合材料の間に挟む
ことでサイズ□50x35mm程度の接合まで可能となります
【関連装置】
・DMB接合 :超音波金属接合装置 UB5000/3000/2000LS
<フレキシブル基板接合技術>

従来工法によるフレキシブル基板接合は基板の間にACFを挟むため、接触抵抗が生まれ、抵抗が高くなってしまいます。
一方、超音波によるフレキシブル基板接合では、ACFを介さず基板と金属部同士をダイレクトに接合できるため、
接触抵抗が低く、COBやCOF、FOB(写真中央左)、FOF(写真左)といった分野に活かすことが可能です。
【超音波接合のメリット】
1.短時間接合
●超音波接合による接合時間は0.2~1sec程度で、樹脂溶融・硬化が必要なACF接続に比べ大幅に時間短縮が可能です
2.常温接合
●超音波は常温で接合できるため、材質ごとの線膨張係数の違いによるライン&スペースの誤差を考慮した
基板設計を行う必要がありません
3.低接続抵抗
●超音波接合では、ACFを介さず基板の金属部同士をダイレクトに接合できるめ、ACF接続と比較し、
接続抵抗72%低減を実現しました(弊社TEG基板による比較)
※超音波接合を行うには、フレキシブル基板にバンプを形成させる前加工が必要となります(写真中央右、右)
【関連装置】
・FPC接合 :スタンドアロン超音波金属接合装置UB500/300/050SA
・FPC接合(量産) :超音波ボンダFB2000SS
<超音波カット技術>

1.軟質多層材カット(写真左)
●超音波カットは上下振動により断続的にカットするので、層間引きずりのないカット断面を実現します
2.グリーンシートカット(写真中央左)
●超音波振動の印可により、グリーンシートの切断面の変形が抑制され、微細な部品の切り出しと
厚い部品の垂直カットを可能にします
●グリーンシートカット専用装置は画像処理機能、及び搬送Y・θ軸を備え、量産対応を実現します
3.TIM(Thermal Interface Material)スライスカット(写真中央右)
●超音波振動印加によりTIMの弾性変形を抑制することで、従来困難だった0.1mm以下のスライスカット
を実現します
●スライスカットした製品をコンベア搬送して収納する量産装置の実績も多数ございます
4.活物質塗布電極カット(写真右)
●超音波振動印可により切断負荷を抑制し、バリのない形状カットを実現、
活物質のように脆い素材も壊さずにカットできます
●ロールtoロール搬送を備えた量産装置の実績も多数ございます
【関連装置】
・軟質多層材カット :超音波カッターUC1000LS
活物質塗布電極カット
・グリーンシートカット :グリーンシートカッターGC1000MS
・TIMスライスカット :超音波カッターUC1000LS(精密スライス仕様)